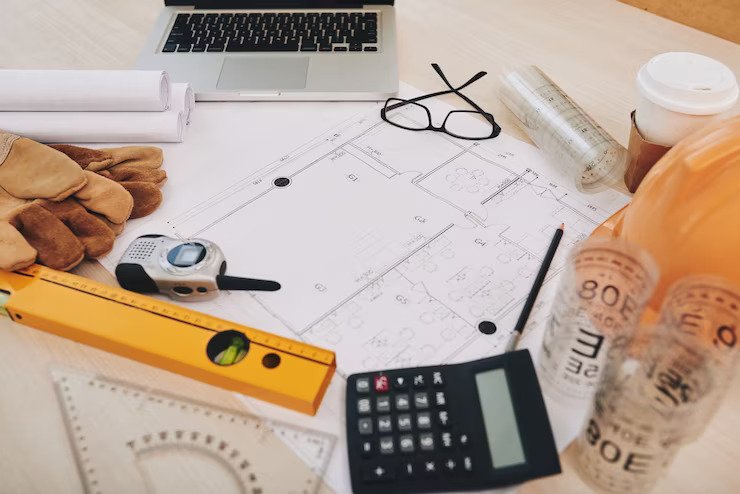
It can cost anywhere from $178,000 to $416,000 to build a house—but that’s too vast of an estimate to give a client if you’re trying to win a bid as a contractor. After all, there’s an enormous amount to consider, from purchasing the initial plot of land to expenses such as hiring multiple large dumpsters designed for commercial and construction site jobs. You therefore need to make your quotes as accurate as possible to give you the best chance of success. Otherwise, you’re going to struggle in what can prove to be a very competitive market!
So, how do you figure out the material and labor cost for a construction project? Traditionally, you could only do this manually. From determining the daily wage of labor to finding out how much materials cost, you had to do it all on paper. Today, software and AI applications can help you make accurate calculations.
But even with these advancements, you should know the basics of calculating a construction project’s cost. This guide will help you learn that.
3 methods to calculate labor and material costs in a construction project
There are three general ways to calculate the material and labor costs of a construction project. We explain each of them in detail below.
1. Unit pricing method
The unit pricing method is best suited for bid estimates and project designs. You can use it to calculate labor costs for your project.
Here’s a simple example. Suppose you need to build a wall. Ten people are required for the job. The average hourly rate for each individual is $30, and it takes 10 hours to build a wall.
You can multiply these figures to get the labor cost for building the wall. In this case:
10 x 10 x 30 = $3800
You don’t have to wing or estimate the labor costs for each type of laborer. Instead, use the data from the U.S. Bureau of Labor Statistics for accurate calculations.
How to use unit pricing for materials and labor?
If you’ve done projects in the past, you can use historical data to estimate how much labor you’ll need for each project. Alternatively, use a cost database.
A cost database is a cost reference book that keeps internal records for labor and material from an agency or a company. Some cost databases are commercially published, allowing anyone to access and use them.
Federal agencies often collect data from construction partners, specialists, and vendors to create their own cost databases. This data can provide a reliable benchmark to estimate labor and material costs for similar projects.
Another alternative is to calculate the unit price for your project yourself. Here’s how to do it:
- Select an assembly item, such as a roof. Calculate the labor costs for building it by multiplying the time required for assembly with the direct labor hourly rate. For example, if the direct labor hourly rate is $300 ($30 for ten workers), and the time needed for assembly is 36 hours, then the labor costs for that assembly item will be $10,800.
- Then, calculate your material costs.
- Add the labor and material costs to get total direct costs.
- Divide this figure by the total square foot of the assembly item. Suppose the roof is 100 square feet. The cost per square foot of the assembly item will be $108.
- Add 10% for productivity and waste.
Now, you have the cost of building a roof. You can add it to your database and use it for subsequent projects. You have to calculate the costs for all assembly items to get the whole cost for the project.
2. Square foot method
The square foot method is a quick and useful way to calculate materials and labor costs, especially for last-minute bidding. But you must have historical data for it.
Here’s how to do this:
- Take out the records of all your previous construction jobs.
- Assign a type to each job. Some examples include apartments, tenant build-outs, residences, and commercial buildings.
- List the size in square feet for each project. In the next column, list the contract value.
- Divide the contract value by the size in square feet to get the cost per square foot.
Suppose you have done three projects in the past. Their data lays out like this:
Project Type | Contract Value | Size (square feet) |
Apartment | $3,000,000 | 18,000 |
Apartment | $4,200,000 | 32,240 |
Apartment | $3,200,000 | 18,400 |
The cost per square foot for these apartments is $166, $130, and $174, respectively. Find the average of these costs to determine the cost per square foot of building an apartment, which is $156.6 in this case.
But how do we differentiate between the cost of labor and material? Usually, 40% to 50% of a construction’s cost is labor. The rest is material.
3. The rule of two
The rule of two follows the principle that labor accounts for 40% to 50% of a construction project. If you’ve done enough projects or are using a project database, you can use your labor costs to calculate the material costs.
For example, if your historical data shows labor costs for building a house are X, multiply X by 2 to get the total construction cost. Also, add 10% of this to the final cost for any unforeseen costs.
How to use construction software to calculate labor and material costs?
Construction software can streamline cost calculation by giving you advanced tools and pre-defined templates or cost assemblies. Some features of such software include:
- Real-time tracking – Most construction software tools let you track costs in real time. You can easily add labor and material costs to the project with a few clicks.
- Pre-defined assemblies – These tools often have built-in project cost databases and assemblies to help you calculate project costs.
- Unlimited timesheets – You can create unlimited timesheets for all projects. These tools let you track payroll, insurance costs, and employee hourly wages.
- Custom templates-These tools let you create custom templates for all projects, allowing easy and quick cost estimation.
You can also store historical data in construction software and use it for all your future projects.
Conclusion
Regardless of the method you use for labor and material cost estimation, you should account for unforeseen circumstances and cost hikes. Even if your cost calculations are not accurate to the T, they should give you a general idea of the budget to quote to a project owner.
Keep track of all project costs to create a cost database of your company for subsequent projects.
Read Also: