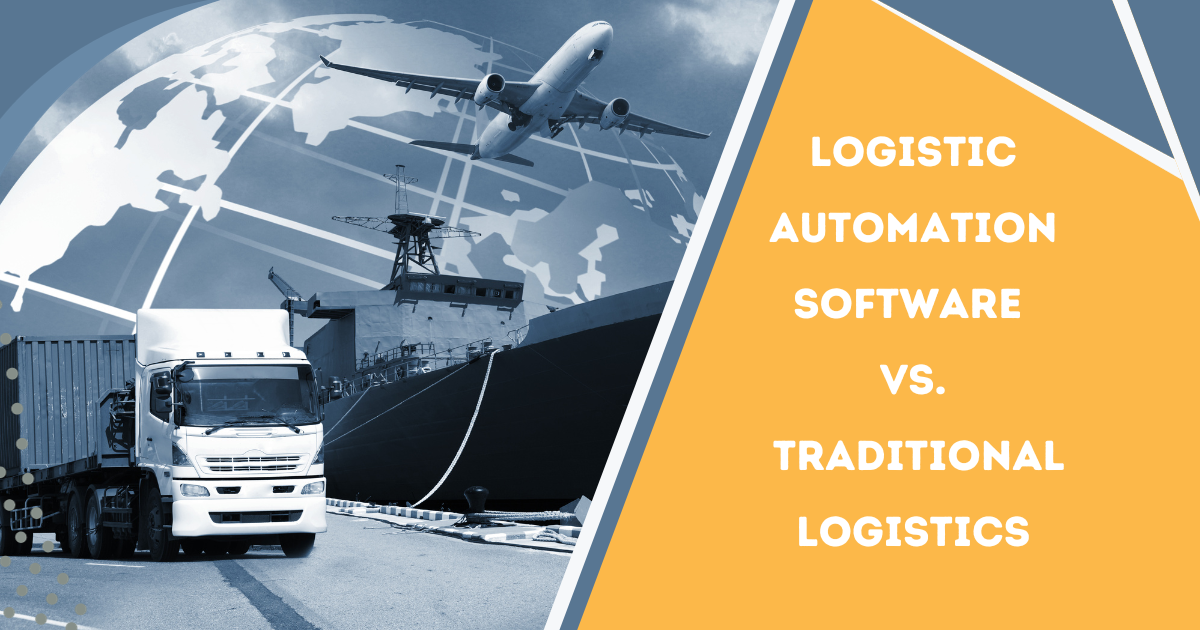
The logistics business is going through big changes. Moreover, the new technologiesand automation solutions are causing the changes. Logistic automation software is transforming traditional logistics. It brings new efficiencies to supply chain management.
This article compares logistic automation software to traditional logistics. It looks at key factors.
The Evolution of the Logistics Industry
Logistics play an important role in business and the economy. The global logistics market was worth $4.96 trillion in 2020, accounting for 8-10% of the total cost of the average product. This shows the huge size of logistics worldwide.
For decades, companies used old logistics models. Moreover, these focused on manual work, paper documents, and broken-up systems. While these old practices started the industry, they have problems and waste. As customer expectations rise and global competition intensifies, businesses are seeking to enhance their logistics capabilities.
This sets the stage for new solutions like logistic automation software. Also, the use AI, machine learning, robotics, and IoT to reinvent supply chain processes. The logistics automation market is predicted to grow by 10.6% annually from 2021 to 2028. Hence, companies are making automation and digitalization a priority.
Key Benefits of Logistic Automation Software
Logistics automation software offers quantifiable advantages and improvements compared to traditional logistics models:
Cost Savings:
Manual supply chain processes take lots of staff time across sourcing, warehousing, order fulfillment, and delivery. Employees doing paperwork and procedures by hand is expensive. Automating tasks with software, AI, and robots slashes those labor costs. Streamlined automated operations also reduce costly errors and waste. Some estimates show logistics automation can lower total supply chain costs by up to 30% for companies. These are significant savings that directly impact the bottom line.
Increased Efficiency:
Order processing and inventory management tasks get done 15-20% faster with automation. Picture an online order coming in. Automated systems can instantly check product availability in the warehouse, reserve inventory, issue picking instructions to robots and process shipping labels. That’s far faster than human workers phone calling, passing paperwork, and managing spreadsheets. Faster logistics throughput directly improves customer service and satisfaction.
Better Accuracy:
Even the best employees make mistakes when engaged in repetitive manual tasks such as order picking and data entry. Automated systems use sensors, scanners, AI, and real-time data to eliminate most errors. One survey showed that 63% of supply chain professionals reported better inventory accuracy after adopting automation tech. Accurate logistics ensure customers get the right items in the right quantities every time.
Scalability:
Companies can effortlessly increase automated capacity to accommodate a higher volume of orders, additional warehouse locations, more transportation routes, and increased delivery demand. Unlike humans, software and robots don’t require hiring, training, or supervision when workloads increase. This seamless scalability supports business growth into new markets and geographies without the need for significant labor additions.
Adaptability:
Machine learning algorithms constantly refine warehouse automation to maximize throughput. Routing software adapts distribution routes in real-time based on traffic and weather. Automation delivers the flexibility needed to meet changing customer requirements and market conditions quickly.
The Strengths and Limitations of Traditional Logistics
While automation delivers tangible improvements, traditional logistics still have some unique strengths:
- Proven practices: Mature processes based on industry knowledge and best practices. Workers know these proven methods.
- Human touch: People doing tasks allow nuanced decision making and quality control. This can help with specialized or new processes.
- Lower startup costs: Traditional operations don’t need big investments in new software, hardware, and integration. The costs are limited to manual labor and transportation.
However, traditional logistics also come with inherent limitations in today’s technologically driven landscape:
- Higher long-term costs: Manual processes need more workers and resources. This leads to higher costs over time despite lower startup investments.
- Lack of scalability: It is hard to quickly scale up traditional logistics across regions and suppliers without proportional investments in labor and infrastructure.
- Limited agility and visibility: Broken-up processes and paper tracking reduce company-wide visibility. This makes it harder to respond to changes or disruptions.
Key Factors Impacting Automation Decisions
Businesses should weigh several factors when assessing automation opportunities:
- Company size – Large corporations with offices around the world often have complex logistics needs. They move a lot of goods and data worldwide. For them, automation makes sense because they have the money to invest in it. Small local businesses may not need automation across everything they do. But they could still benefit from automating some focused areas, like inventory management.
- Industry – Some industries really stand to gain from logistics automation. E-commerce companies that ship tons of online orders can speed up warehouse picking and delivery routes. Pharmaceutical firms need to track temperatures and shipping times. Electronics makers have complicated supply chains. Automation helps these industries handle all that complexity smoothly and quickly.
- Distribution network – Companies with huge warehouses or big fleets of trucks and planes could maximize automation in those assets. Automated warehouse robots and GPS fleet tracking offer major advantages. Firms with smaller logistics operations may not get as much value from large-scale automation.
- Cost reduction goals – Logistics make up a huge chunk of overall expenses for many companies. Automation often slashes those costs over the long term, which is super appealing. But businesses content with current costs and profits might not want to rock the boat.
- Competitive pressures – Rivals adopting slick new automation force everyone else to keep up. Plus, customers want faster, more customized service through automation. Embracing the latest logistics automation can assist companies in maintaining a competitive edge.
Implementing Logistic Automation Software
Migrating manual logistics operations to automated systems is a multi-step process:
- Analyze logistics processes to identify top automation opportunities. Focus on pain points and waste.
- Research vendors and software solutions that address your needs across order management, inventory, warehouse operations, transportation, and delivery.
- Start with a pilot project focused on a contained process like order fulfillment. Measure results before expanding the rollout.
- Evaluate infrastructure needs like connected sensors, mobile devices, robots, and conveyor systems to support software integration.
- Develop a training program to reskill staff on using and managing the automation technology.
- Continuously assess performance metrics. Use insights to optimize the automated processes.
Frequently Asked Questions
What are typical costs of implementing logistic automation?
Costs vary a lot based on scope, technologies used, infrastructure needs, and customizations. Large corporations see investments from $10 million to over $100 million. However, focused solutions for SMBs can cost less than $100,000.
Can traditional and automated logistics co-exist?
Yes. A hybrid model allows companies to gain automation benefits in targeted areas while keeping traditional operations where manual work is preferred. This phased approach facilitates the transition.
What risks come with logistics automation?
Automation leads to concerns like IT security, system failures, integration with old platforms, and loss of human oversight and jobs. These require strong change management and security controls. But the long-term gains outweigh the risks.
Bottom Line
In summary, logistics automation delivers transformative performance, cost, accuracy, and flexibility benefits. But some human judgment and oversight will remain beneficial.
Companies that adopt a balanced approach can harness the benefits of automation while mitigating risks through effective change management and training.
Read Also: