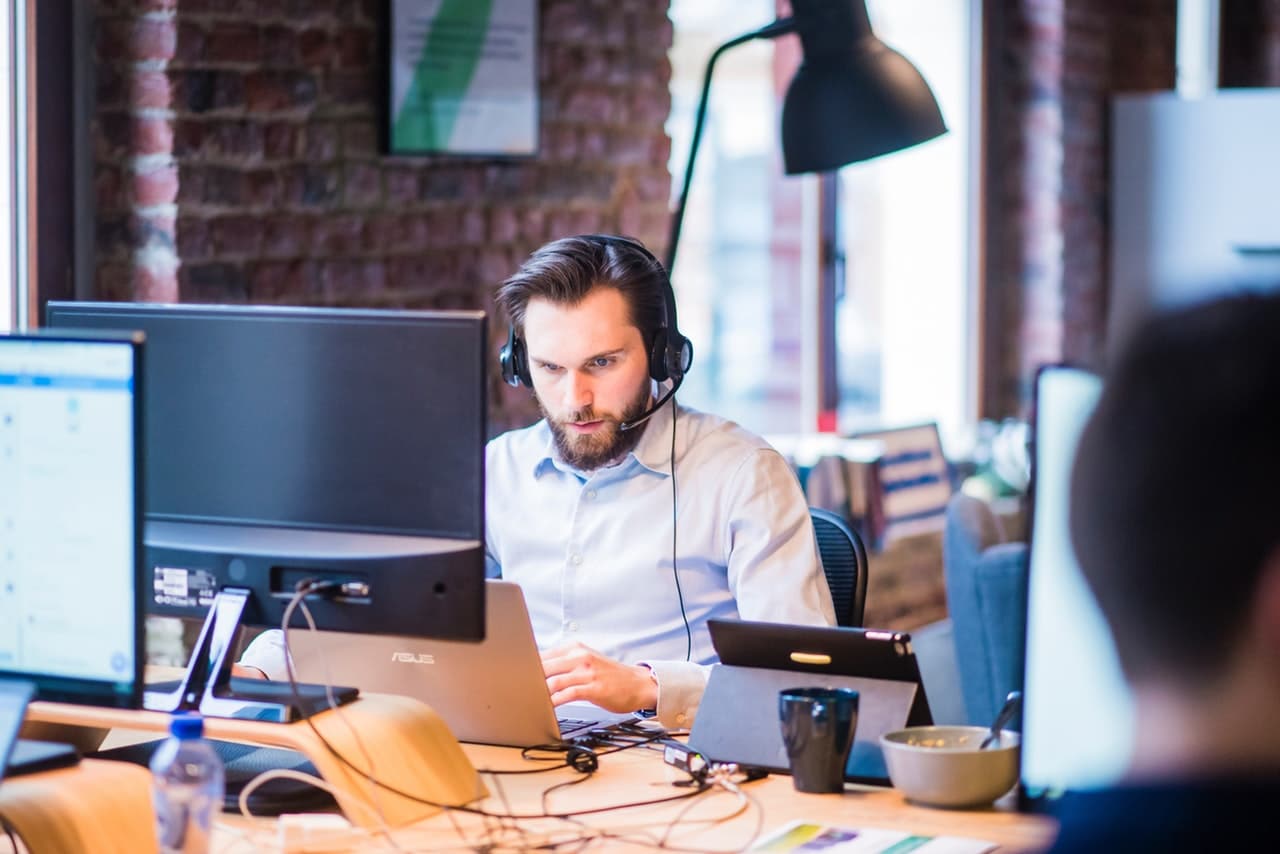
Famous British economist John Maynard Keynes made a very famous quote that meant something along these lines – “All machines break down in the long run”. Even if it is a gross reinterpretation of the original quote, there is an iota of truth to it.
It is a known fact that all machines are prone to wear and tear. To further reiterate this fact, a study by Emerson and the Wall Street Journal found that it cost industrial manufacturers $50 B USD due to unplanned downtime. 45% of this unplanned downtime was because of equipment failure.
This is a massive loss. What can be done to prevent this?
The answer to this is to bring in place an equipment maintenance strategy that is extremely efficient.
The early stages of the industrial revolution did not have complex machines, and this meant a lesser number of breakdowns. The scenario today has changed with the advent of the assembly line as well as automation via PLCs (Programmable Logic Controllers).
Manual labor today has lessened, and automation has increased. Apart from automation, factories now measure and closely track different other metrics like equipment effectiveness, production output, personnel productivity, etc.
Maintenance which was seen as something that was required only when there was a breakdown of machinery. Today, it has assumed a lot more importance. The importance of preventive maintenance being scheduled regularly has become a popular strategy. This ensured periodic inspections of machinery that helped identify issues early which led to breakdown minimization and reduced production stoppages.
A greater focus on operational cost, equipment utilization, worker productivity etc are given as we enter the next stage of the industrial revolution which is Industry 4.0 or Industrial Internet of Things (IIoT).
Connecting low-cost sensors to gather data from machines and using advanced analytics to decipher meaningful insights is what the Industrial IoT is about. Industrial IoT will now allow manufacturers to boost their productivity by 30%. The maintenance strategy employed which uses advanced analytics to predict failure of machines is predictive maintenance.
Steps to be taken before implementing a predictive maintenance program:
- Analyze equipment history and the need
- All available records on equipment defects, downtime, possible regulation fines, losses, and workplace safety should be reviewed thoroughly
- Clearly establish definitions and concepts and also build a case for predictive maintenance
- The major stakeholders must be educated regarding the program
- Equipment inventory must be completed, and the current condition of the equipment should be appraised
- Equipment should be selected for the initial program implementation
- System details should be developed based on individual components
- Evaluate existing preventive or predictive maintenance programs
- A decision as to which systems need to be included and what needs to be inspected should be made.
- Predictive maintenance frequency and schedule should be defined along with the program criticality
- Roles and responsibilities should be assigned after evaluating the resources
- Organize the program and integrate it with the scheduling system
- Educating and obtaining buy-in from operations and maintenance
- Upgrade the equipment and conduct training
- Create a computerized maintenance management system (CMMS)
Predictive Maintenance and IoT
In a successful predictive maintenance program, the use and integration of IIoT is the most important factor. A report by Deloitte tells us that the internet of things is the most important part of the predictive maintenance puzzle.
Physical actions from machines are converted into digital signals with sensors like conductivity, temperature or vibration by IoT. On conversion of these physical actions into digital signals by the sensors, they are then processed, accumulated and analyzed. With enough storage and bandwidth, large amounts of data can be transmitted which will not only give you the entire picture of assets in one plant but of the whole production network.
The World Economic Forum conducted a survey which concluded that predictive maintenance is the biggest application of the Industrial IoT. The advantages that predictive maintenance offers manufacturers is extended equipment life, low maintenance costs, and reduced downtime. Predictive maintenance helps improve production quality by dealing with problems much before they cause equipment failure. To reap these benefits, a strong digital infrastructure needs to be in place. This should include a platform deployment like the Microsoft Azure Suite combined with the use of predictive modeling and machine learning to properly analyze machine data.
For predictive maintenance to be successful, it relies heavily on the sensors that accumulate and analyze data from multiple sources like CMMS or critical equipment sensors. Making use of this data, the program will now be able to create advanced prediction models and advanced analytical tools which will predict equipment failure and allow us to address them proactively.
The performance of the predictive maintenance model can be increased with the use of machine learning which will, in turn, increase the accuracy of the predictive algorithms.
Predictions made better in predictive maintenance
Predictive analytics makes use of past data to help predict future outcomes. Predictive analytics, however, is not the end result but is the journey leading to it. The right set of data points need to be identified.
These data points need to be integrated with the machine in order to ingest data in real-time. This will then improve the quality of the data via live tracking of equipment failure. For any predictive model to be accurate, data preparation and quality of data are the key inputs. Better accuracy can be achieved with more high-quality data being fed.
IIoT, when paired with predictive maintenance, allows for equipment failure to be caught in advance. With the advent of Industry 4.0 in the manufacturing sector, organizations are making use of advanced analytics, prediction as a part of their predictive maintenance programs to gain better insights into their operations and reduce costs.