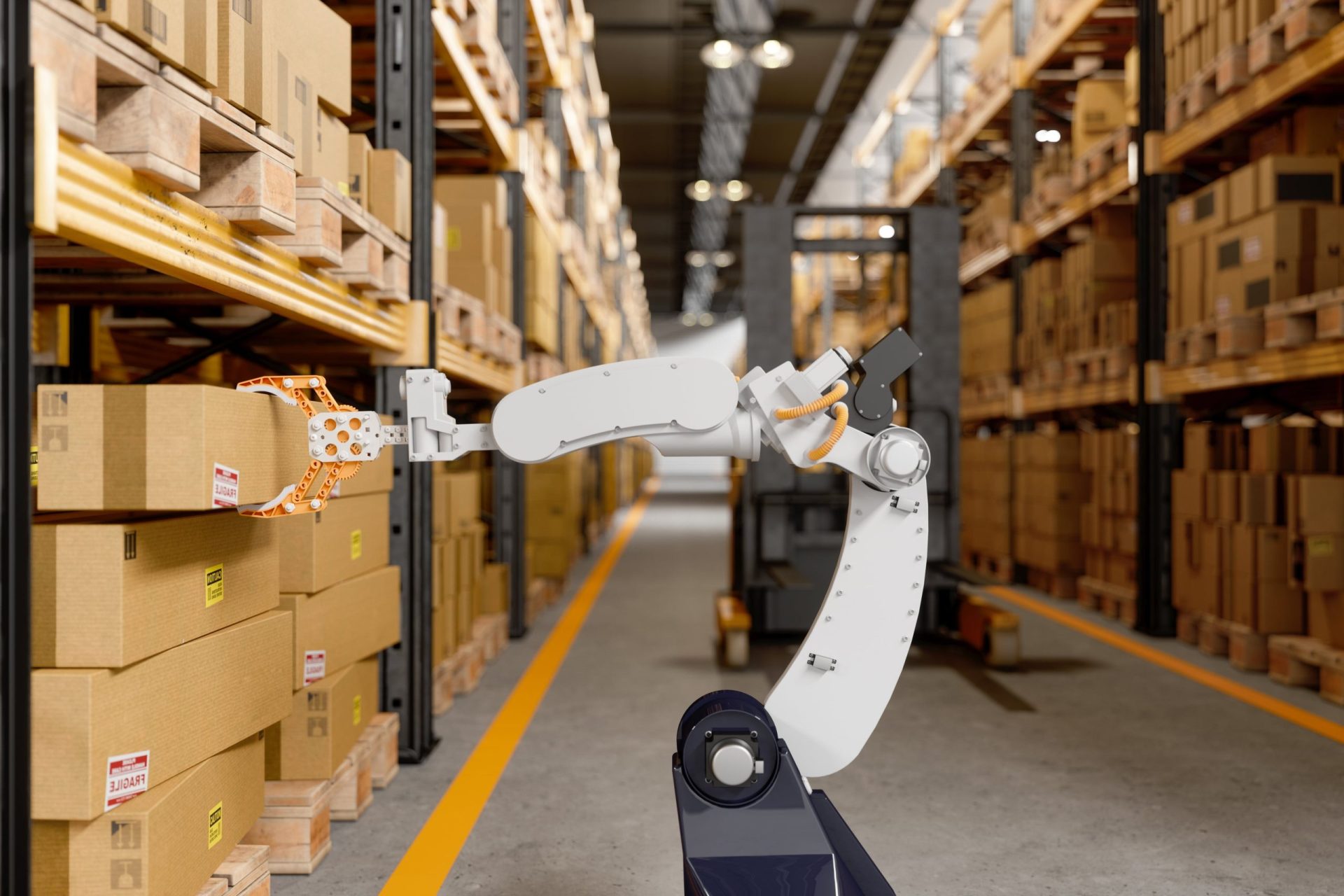
There are a lot of dangerous jobs out there, particularly in industries involving heavy machinery, repetitive tasks, or those involving difficult environmental conditions. Even if the job itself is not inherently dangerous, a human worker who may be tired or inattentive can create a dangerous situation or potential hazard for themselves or those around them. What about robots? They can do the work as humans, and we all know robots are not humans, so you can minimize the chances of an accident.
Let’s take a look at how social robot development is universally improving working conditions in some of the most dangerous industries.
What Are The Most Common Workplace Injuries?
Imagine a world in which workplace injuries were a thing of the past; no lost time accidents, no dips in production, no lost time wages paid, and, above all, no more workplace casualties.
While workplaces around the world continue to innovate in order to make this world a reality, the truth is there is much to do before injuries suffered at work are a thing of the past.
Robots, of course, will play an important role in bringing those numbers to zero, but before anything can be done, it’s important to understand the most prevalent injuries suffered by workers in the workplace.
- Trips, slips, and falls
- Being struck by moving machinery
- Getting caught in machinery
- Accidents related to moving vehicles
- Fires/explosions
- Repetitive stress injuries
How Are Robots Making Things Better For The Average Worker?
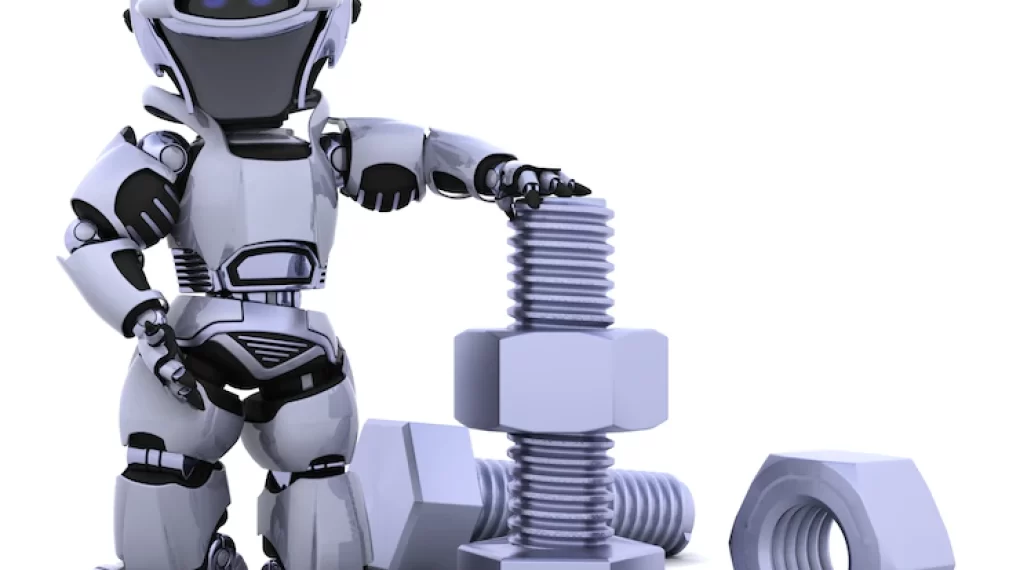
Many people view the propagation of robotics as a sign that the days of the human worker are numbered. In fact, that has never been the end goal of any field of robotics. Industrial robot uses have been popular in American workplaces for many decades. The Robotic Industries Association estimated in 2017, more than 250,000 such types of robots had been installed in the United States.
These machines bear little resemblance to their science-fiction counterparts. Usually, these are more like forming of strong, heavyweight AI-powered arms that perform tasks such as welding, painting, or assembling within the confines of a cage or other enclosure. Recently, however, technological advances have begun to allow for a greater diversity of robotic systems in the workplace.
New Roles For Robotics
According to Bob Doyle, Vice President of RIA, industrial robotics have traditionally been used to complete tasks that he claims fall squarely into the realm of “the three Ds – dull, dirty, and dangerous.” It’s not unsurprising, then, that as the number of industrial robots deployed to perform these tasks continues to grow, the inverse relationship between robotics and workplace injuries becomes clearer.
Greater, More Robust Safety Standards
If you’ve ever seen an industrial robot in action, you will understand why they are typically designed to include a wide berth. While these machines do bolster productivity and reduce certain injury types, the lack of sensory technology in these robots means that these devices can pose a danger to humans (but more on that later).
Fortunately, modern industrial environments have never been safer thanks to nationally and internationally agreed-upon standards that govern the use of industrial robotics.
Current safety standards like ANSI/RIA R15.06 and ISO 10217 have even been amended to include the introduction of collaborative robots, or cobots, something that is undeniably important given that cobot are designed to work collaboratively with human workers,
International standards aside, governments are also making strides to make the use of robotics safe for all those working under the same roof; the National Institute for Occupational Health & Safety (NIOSH) formed the Center for Occupational Robotics Research (CORR) in 2017. Put simply, the priorities of CORR are:
- Identifying opportunities to better protect worker safety and health using robotics
- Increasing understanding of human and robot interactions to ensure human worker safety
- Improving the ability to identify and track injuries and fatalities involving robotics
- Providing guidance on working safely with robotics
Building A System That Is Inherently Safe
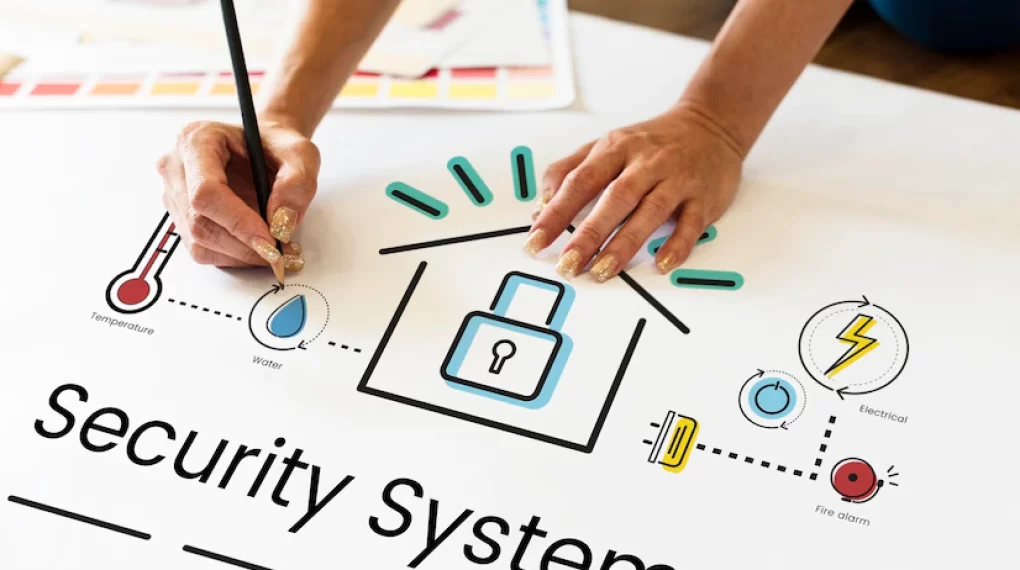
Cobots, in particular, due to their use in proximity to humans, are designed around a number of safety features. Even with these safety measures in place, there is always the possibility of an accident occurring. Since every cobot and every working environment is different, it is imperative that risk assessments are conducted to safeguard against potential threats of injury. It is equally important that these assessments are a core requirement for the robots and cobotic deploy.
Read Also: Top 5 Technological Trends To Watch Out For In The Future
Do Robots Themselves Pose A Hazard?
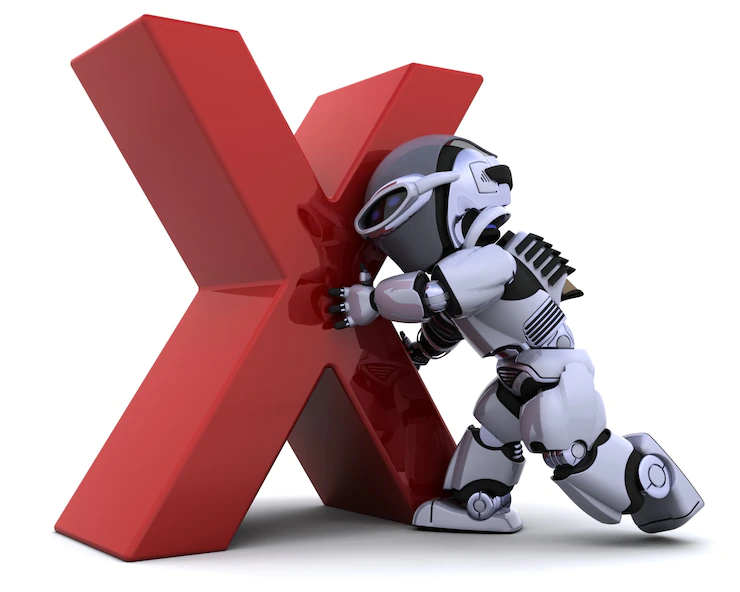
As alluded to above, the short answer is yes; the use of robotic technology, though it is designed and implemented with worker safety at the top of its mind, is not without its risks. Workplace fatalities can still arise using robotic machinery.
One such case involved an employee at a bottling facility who was crushed by an autonomous Laser Guided Vehicle, or LGV. LGVs are driverless vehicles often used to transport materials or finished goods from point A to point B, similar to how a forklift is used to deliver pallets of goods from one place to another.
As you would expect, LGVs are loaded with sensors that allow them to navigate through an ever-changing environment that includes humans. These sensors are supposed to detect obstacles and stop the vehicle before contact is made.
Before clearing the obstruction from the path of the LGV, the worker is supposed to initiate an emergency stop that would prevent the LGV from immediately continuing its journey once the object is no longer detected by the sensor.
In the case at the bottling facility, the worker did not initiate the emergency stop before clearing the object from beneath the LGVs forks and was subsequently struck by the vehicle.
The point is that even if the robotic device is operating correctly and as intended, there is still the possibility of injury.
While these types of robots related injuries remain rare, there are other hazards that workers should be mindful of when working around robotics:
- Ergonomic injuries resulting from using new robotic machinery
- Injury resulting from human error, including a lack of understanding of required safety protocols
Bottomline: There Will Always Be Danger, But Less So In The Presence Of Robots
There is no denying the modern workplace is safer than ever before, but it’s still not without its dangers. Through the continued improvement in universal standards and the widespread adoption of robotic technology, many of the existing threats can one day be eliminated.
Robots, like their creators, are not perfect, but they are the best-emerging tool that industries can leverage to protect their workers and their businesses. If you’d like to learn more about robotics and the wide and varied careers that are available, check out this online education program.
Additional: