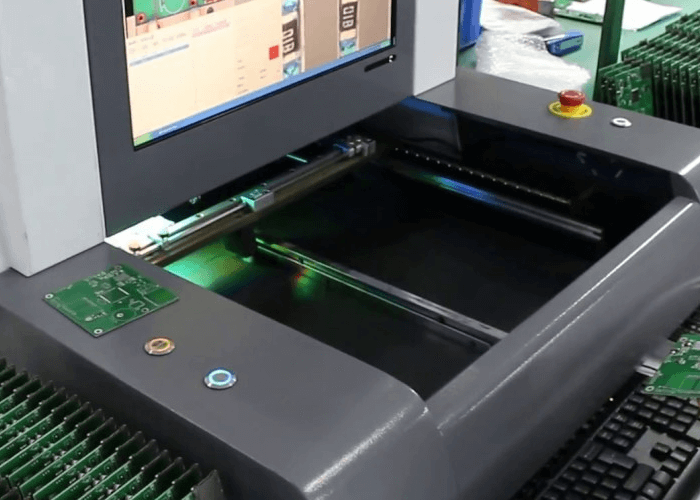
The complexity and density of printed circuit boards nowadays make the use of optical inspection machines (AOI) more and more indispensable. Human controls and inspections have become insufficient as they are prone to error and are too tedious.
To improve PCBA production quality, OEMs require good wafer inspection. EMS providers are increasingly taking advantage of advanced AOI inspection technology with numerous benefits to ensure efficient and detailed review of SMT PCBs.
In this article, we are going to talk about the use of AOI systems in the SMT process. Let’s get right to it.
Virtually every current electronic device works with a printed circuit board. PCBs connect electrical components such as integrated circuits (ICs) mounted on bare boards used in various electronic devices, including notebook computers, electronic watches, calculators, electronic communication equipment, and more.
Due to the progressing miniaturization, these components are currently assembled with the SMT surface mounting method. Therefore, to find out why professional EMS suppliers test PCBs using the AOI method, we need to look closely at the SMT assembly technology.
Surface Mount Technology (SMT)
Surface mount technology is a component assembly technology compared to printed circuit boards. It varies from its predecessor: through-hole technology (THT) in that instead of routing wires through holes drilled in the PCB, components, and elements are mounted directly to the surface of the PCB.
Due to this, SMT assembly allows higher packing density, product reliability, and lower cost than previous assembly methods. SMT also offers a better presentation of the structure of printed circuit boards.
Here you can find more information: https://asselems.com/en/smd-assembly
Today, surface mount technology is the most widely used process for high-performance consumer electronics components. There is no doubt, however, that this is not an ideal solution without disadvantages. For example, the more progressive miniaturization of elements and their high density on the PCB surface makes repairing potential errors or defects much more difficult. That is especially problematic at the end of the assembly process.
The necessity to conduct checks
To eliminate unwanted incidents early, EMS companies perform high-quality controls and inspections throughout the entire production process. As a result, they can guarantee OEMs that the PCB has no defects and can be used in other production processes.
There are many types of inspection and control. One of the most popular ones so far has been manual control, which is no longer desirable due to its unreliability resulting from the possibility of human error and the economic aspect.
These types of tests take much longer and therefore generate much higher costs. Suitable EMS suppliers know the importance of speed and accuracy in inspecting all electrical assemblies, especially PCBs, so they use an Automatic Optical Inspection (AOI) solution.
AOI Inspection Characteristics
AOI provides a way to check for common PCB defects such as missing or incorrect parts, incorrect element orientation, lower solder quality, and lead bridging.
Automatic Inspection Optical looks for flaws and faults in the initial production process of printed circuit boards. AOI uses optics to capture and analyze PCB images.
Thus, it becomes an indispensable element of contract assembly, increasing the quality of services offered and production efficiency. It uses new constructions of measuring heads, miniaturization of equipment, software processing the obtained images of plates, and complex algorithms for image transformation.
With the help of the AOI method, EMS suppliers can verify the correctness of electronic components assembly in terms of:
- Presence and correct alignment of elements on the board, including the arrangement of components along the horizontal and vertical axis
- Quality of welds of multiple components (solder joints and bridges)
- Polarity
- Labeling of individual details,
- Flux deposits
- Subsurface defects and Microcracks
Depending on the expected result of the inspection, AOI devices equipped:
- High definition camera or cameras (alternatively infrared camera)
- Numerous light sources such as LED lighting, infrared lighting, or UV fluorescent lighting
AOI 2D and 3D systems, what are the differences?
There are two types of AOI on the market. 2D technology has been widely accepted by EMS providers for many years and has practically become obligatory in most SMT production plants.
On the other hand, 3D technology is younger, but compared to 2D inspection, it enables more accurate measurements and a more stable control process.
2D AOI technology
As 2D inspection methods have been used for many years, much time has been spent developing software interfaces and image processing to simplify the programming process. 2D check cycles are also much shorter as fewer images are captured and processed.
The camera, optics, and lighting used in the 2D system allow for flexible inspection where EMS providers can inspect assemblies with petite and tall components simultaneously.
2D inspection technology, which is cheaper than AOI 3D, is the most common solution used by contract manufacturers and OEMs.
3D AOI inspection
The principal benefit of 3D inspection over 2D inspection is that it gives accurate volumetric height information. A standard methodology used in most 3D AOI systems is phase shift image processing.
With phase shift analysis, you can create a 3D height map and thus regulate the volume of each visible solder joint of each component. Using 3D inspection to detect coplanarity also significantly reduces false joints compared to using 2D inspection.
Of course, the 3D AOI control also has some drawbacks. For example, 3D control approaches cannot check the nomenclature of printed parts, polarization marks, or color.
In addition, more engineering programming work is included in the defect detection process, increasing the associated costs.
What kind of tests to expect from good EMS providers?
To achieve maximum precision and the highest control quality, experienced EMS suppliers combine two AOI inspection methods, simultaneously using two-dimensional (2D) and three-dimensional (3D) control strategies.
There is no doubt, however, that these cannot be the only tests offered by SMT. Thus, an ideal solution for an intelligent electronics factory is using various elements from the 2D AOI, 3D AOI, Solder paste inspection (SPI), Automated X-ray inspection (AXI) toolkit, thanks to which it is possible to ensure high-quality controls and production processes.
Read Also: